When this 400lb monstrosity was delivered to my house, I had no idea how it worked. I’m not gonna lie, I was hoping I could fiddle around a bit, hit play and it would cut like butter. Well…it was a lot more complicated than that. Nonetheless, it's a fascinating machine.
So how does a laser cutting machine work?
Simply put, laser beams blast out of a special tube, bounce off a bunch of mirrors (zing! zing! zing!), pass through a lens, and then burn through your material.
My Machine
There are three main types of lasers, mine is a carbon dioxide laser, more commonly known as a CO2 laser.

Let there be light
The most important component is the laser tube. Mine is a glass tube filled with gas, generally comprised of carbon dioxide, nitrogen, hydrogen and helium. When electricity is shot through this fancy little capsule, a bunch of molecular stuff happens* (you can see how technical this explanation is gonna be). The result? Light.
*Molecular Stuff, if you care
Apparently, the nitrogen molecules get all excited when blasted with electricity. And that gets the carbon dioxide all worked up, bouncing back and forth in the tube like a trapped rat. Then some other molecular craziness happens which I don't get.
Smoke & Mirrors
The generated light beams are directed towards a series of mirrors, 3 to be exact. The last mirror is tilted downwards, towards you material. The light then passes through a lens (hidden in the laser head).
Fun fact: Aligning the mirrors (so the beams land in center) is the most maligned process related to lasers.
The Lens
The lens focuses the beam to create a very precise, hairline cut. As with all lenses, that focal point is crucial. Your material has to be on the same plane as the focal point or else your cut line will be super thick (and won't cut through).

Stay Cool
Blasting energy...laser beams, it's all very hot. To avoid overheating, my machine is cooled with water. Water flows around the laser tube constantly to keep the temperature down.
A fancy water chiller, equipped with an ear-damaging alarm that goes off if the water temp gets too hot, pumps the water through the machine. Like a human heart, the water is pumped, then recycled.
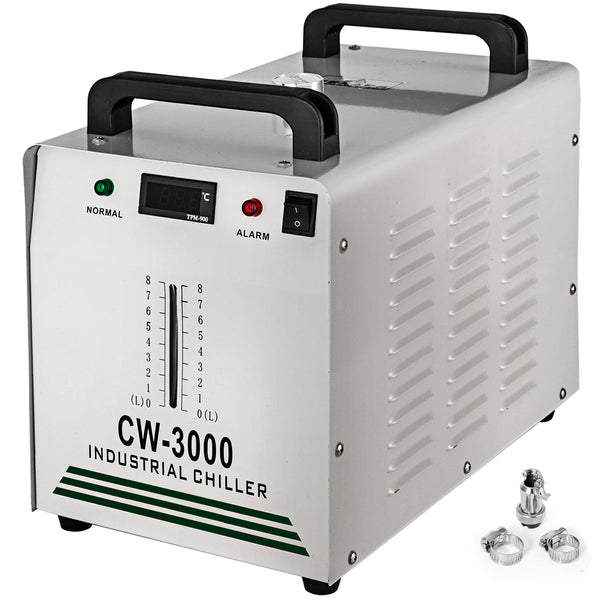
At the laser head nozzle, there’s a tube that forces air onto the surface of the material. This 'air assist' follows every move of your cut, blowing on the material to keep it cool.
Exhaust
The smoke produced by cutting is sucked out of the machine with an air compressor and ventilated.
Honeycomb Bed
It's best to have a honeycomb bed or pin table to ventilate the smoke coming out from the underside of your material. Otherwise, it can’t escape and will overheat, damaging the surface. The honeycomb bed, looks exactly like a car radiator (prob because it is).
My laser is considered a professional machine, I’ve never used a hobby laser. The smaller table-top units seem very convenient, but naturally they aren't heavy duty. I imagine, being so lightweight, they're easy to bump when cutting. I like having my laser completely housed in a metal box for safety reasons, but obviously she's a beast.
What all can it do?
The coolest aspect of a laser cutter is that, in addition to blasting through 1/4" thick material, it can also engrave surfaces. Here's an ornament I designed that uses the image-based etching feature. The engraving process is much more time consuming than cutting. Like a printer, it goes back and forth, etching one sliver of a line at a time.

A laser cutter can cut through materials like wood, cork, rubber, cardboard, paper, fabric, leather and certain kinds of plastics. The limitations generally stem from what is safe to burn.
Etching can be done on even more materials like aluminum, stainless steel, marble, stone, tile, and glass. Believe it or not, I've never tried any of those! Engraving on a curved surface, like a glass tumbler, requires a rotary attachment, which costs a few hundred dollars.
The laser cutter is a versatile machine. It takes a lot more effort than I expected to perfect, troubleshooting can be time consuming, but the capabilities are impressive and offer endless opportunities for creativity.